Compared with other traditional materials, carbon fiber has obvious advantages, such as high specific modulus and specific strength, good mechanical properties of manufactured components, strong designability and high safety, integration of parts and components, and development of a variety of processing The molding process has a wide range of applications in the automotive field. This article introduces the molding process of carbon fiber composite materials used in the automotive field to make carbon fiber molds, and the advantages of carbon fiber composite materials in the automotive field compared to traditional materials. If you are interested in this, then continue to read it.
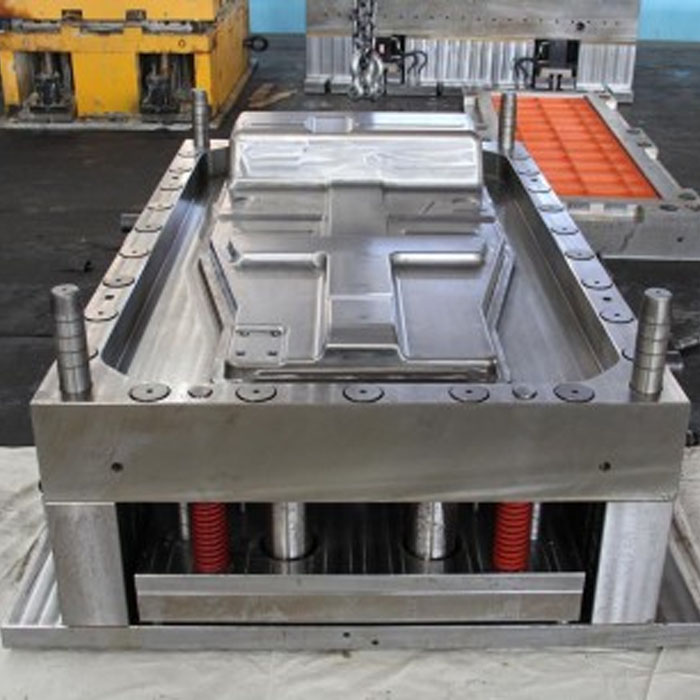
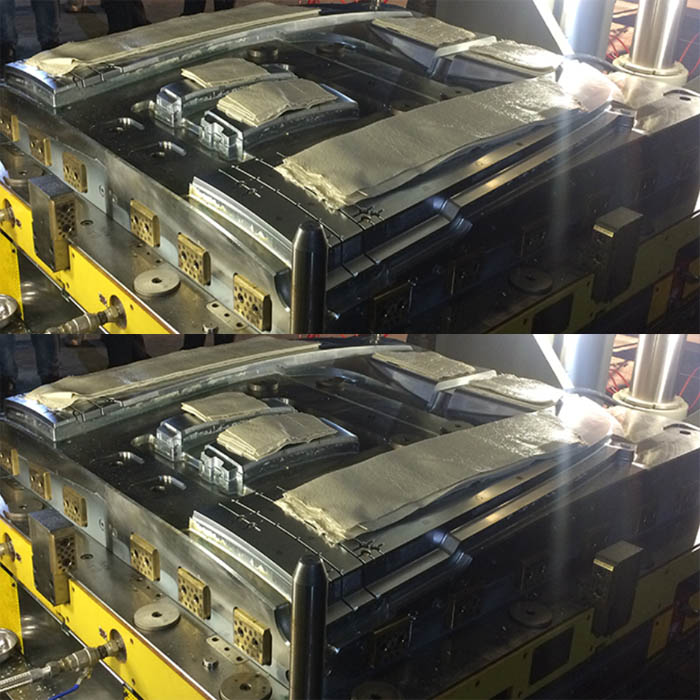
Carbon fiber composite material molding process in the automotive field
1-PCM molding
Compression molding is a molding method in which stamped carbon fiber semi-finished products are placed in a mold in advance, and then heated and pressurized to form and solidify. In recent years, prepregs have been more and more widely used because of their precise fiber and resin ratio. The PCM molding process, as an ideal CFRP tank external hot pressing process, can not only greatly shorten the molding cycle and improve production efficiency, but also has high product dimensional accuracy, good surface finish, relatively low production cost, and easy realization of complex structural parts. Molding and other characteristics. At the same time, due to the good fiber orientation in the product, the strength and rigidity of the product are relatively high, which has become an important molding process for CFRP for vehicles.
2-High pressure RTM molding
High pressure RTM (high pressure rtm, HP-RTM) is an effective method to increase the injection speed by increasing the injection pressure. The injection pressure of this process can reach several gigapascals, which ensures a higher clamping speed and pressing speed, greatly shortens the molding time of parts, and improves the process efficiency. At the same time, increasing the pressure can prompt the resin to quickly fill the mold cavity, increase the fiber resin infiltration, reduce the number of resin injections, promote air discharge, and reduce the porosity of the finished product, so as to achieve excellent surface properties. If you choose to inject a low-viscosity resin system or a low-viscosity reactive mixture system at the same time, the injection speed can be further improved; the precise metering of the reaction materials through high-pressure metering technology can also shorten the injection time.
In addition, due to the strong designability of the structure and performance of CFRP products, when HP-RTM is applied to the manufacture of large and complex structural parts, the advantages are more obvious. The number of firmware simplifies connection and assembly, greatly reduces energy consumption in the production process, and reduces the production cost of carbon fiber molds.
3-Other molding processes
RTM molding process requires high mold manufacturing accuracy, long mold production cycle and high price. The material processing and transportation cost of prepreg is relatively high, and the cost of mold is not low. Therefore, these two molding processes have a large investment in the early stage. . Therefore, other composite material molding processes, such as sheet molding compound (Sheet Molding Compound SMC) molding process, long carbon fiber reinforced thermoplastic (Long carbon Fiber Reinforced Thennolplastics, CF-LFT) injection molding process, have also been widely used. .
MB/Wechat/Whatsapp:+0086-13456489912
sophiemould@foxmail.com
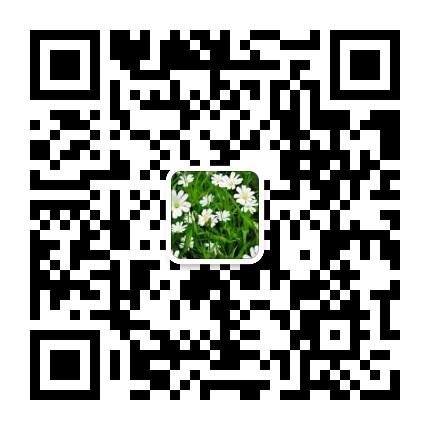
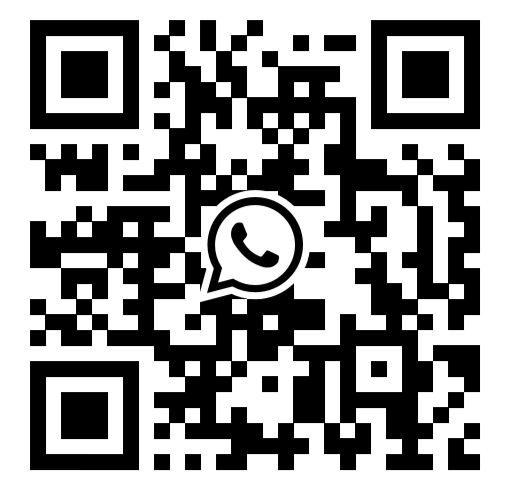
Post time: Aug-20-2021