Place the molded plastic in the cavity of the metal mold, then close the mold under heating and pressurization to make the plastic melt, flow, and fill the cavity. After proper venting, the plastic will be fully cross-linked after the pressure is maintained. Cured into products.
There is no gating system in the compression mould of thermosetting plastics, which saves the forming materials. It is equipped with a cavity or a feeding cavity as a space for holding the forming materials and preheating the materials. The forming pressure is directly applied to the plastic parts by the mold, which is suitable for forming plastics with poor fluidity or with various fillers. In addition, the plastic parts have less oriented organization, low degree of orientation, and more uniform performance in all directions.
There is no gating system in the compression mould of thermosetting plastics, which saves the forming materials. It is equipped with a cavity or a feeding cavity as a space for holding the forming materials and preheating the materials. The forming pressure is directly applied to the plastic parts by the mold, which is suitable for forming plastics with poor fluidity or with various fillers. In addition, the plastic parts have less oriented organization, low degree of orientation, and more uniform performance in all directions.
The working temperature of thermosetting plastic mold is generally 160~250℃, and the unit pressure of the cavity is large, usually 160~200 MPa. Friction occurs between the cavity surface and the flowing powder during operation, which makes the cavity surface easy to wear and bears a certain amount.的; hitting load and corrosive effects. When this type of mold presses various bakelite powder to make parts, a certain amount of low powder filler is added to the raw material, and the molding is formed under hot pressing, so the thermal load and mechanical load are relatively large, and the filler causes the mold cavity to wear out. serious.
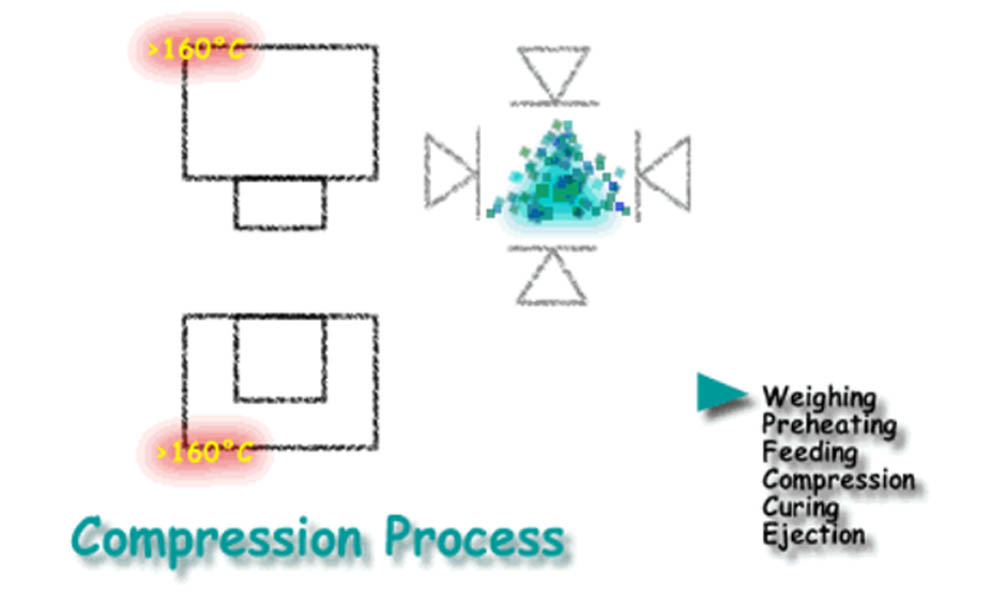
Process characteristics
The molding process and equipment are mature, and it is an older molding process. The equipment and mold are simpler than injection molding.
Intermittent molding, long production cycle, low production efficiency, high labor intensity, and difficult to automate.
The products are of good quality and will not produce internal stress or molecular orientation.
It can suppress products with a larger area, but cannot suppress products with complex shapes and larger thicknesses.
After the product is formed, it can be demoulded while it is hot.
MB/Wechat/Whatsapp:+0086-13456489912
sophiemould@foxmail.com
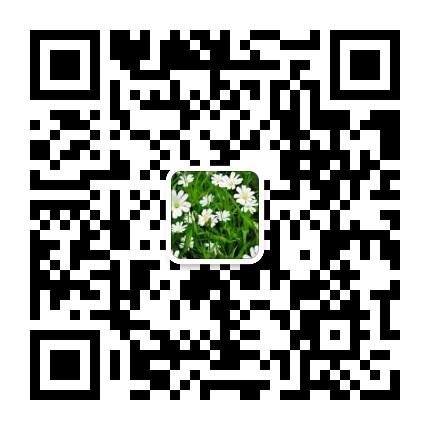
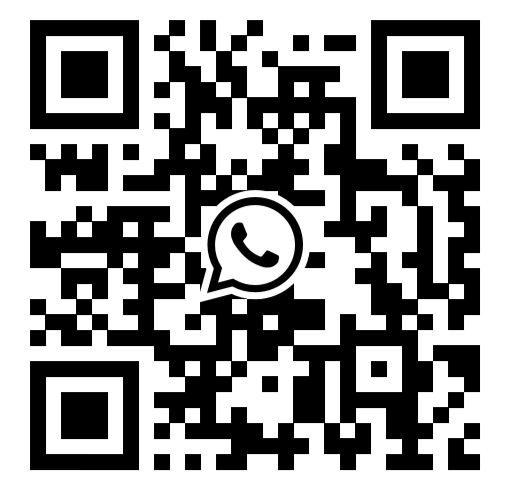
Post time: Nov-26-2021