Mass production of rubber products and plastic products requires molds to be produced. This is the principle of mass production. Rubber molds are mainly based on molded products, so what I will introduce next is molded rubber molds.
Rubber molded products are widely used in industrial applications, and rubber products can be used in almost every industry. The rubber mold is simple and simple, and complex and complex. It mainly depends on the structure of the rubber product. Take a simple rubber gasket as an example. This is the simplest rubber mold structure. There are only two mold templates, which are divided into upper and lower molds, which can also be referred to as concave molds and convex molds. The mold has four guide posts and two mold handles. This is the shape and structure of the mold. The structure inside is similar to the product. Of course, there are also cutting nozzles for the product. This is a simple rubber mold. There are also three-plate molds and four-plate molds that are complex. If the structure is complex and difficult to demold, a mold core is required, and an overturned mold is required.
The product with the highest production capacity is the two-plate mold, followed by the three-plate mold and the four-plate mold. The production capacity of inverted molds with mold cores is the lowest, so the unit price of this type of product is also the highest. Such a mold cannot be opened very large, and if it is opened very large, the production capacity will be very low.
Compared with rubber molds, plastic molds are much more complicated. If you need a hot runner or something, there will be a lot more templates. Plastic molds can also be divided into three-plate molds and two-plate molds.
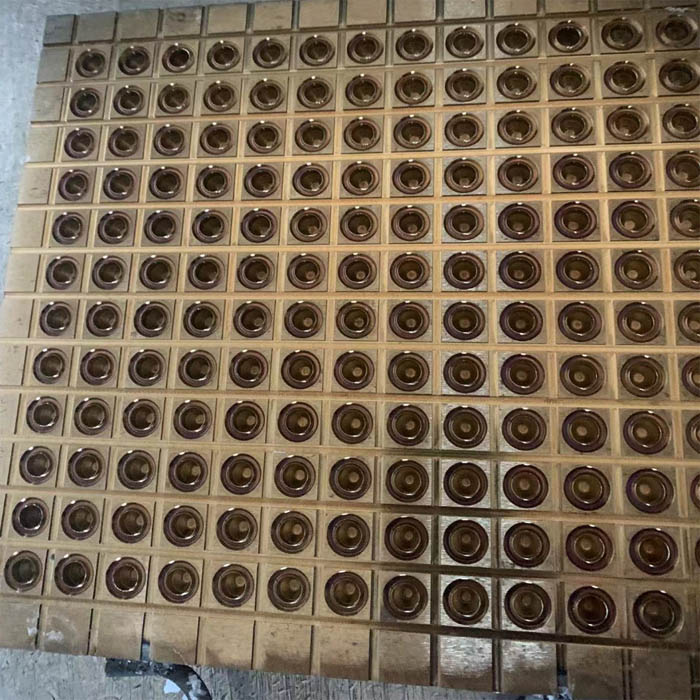
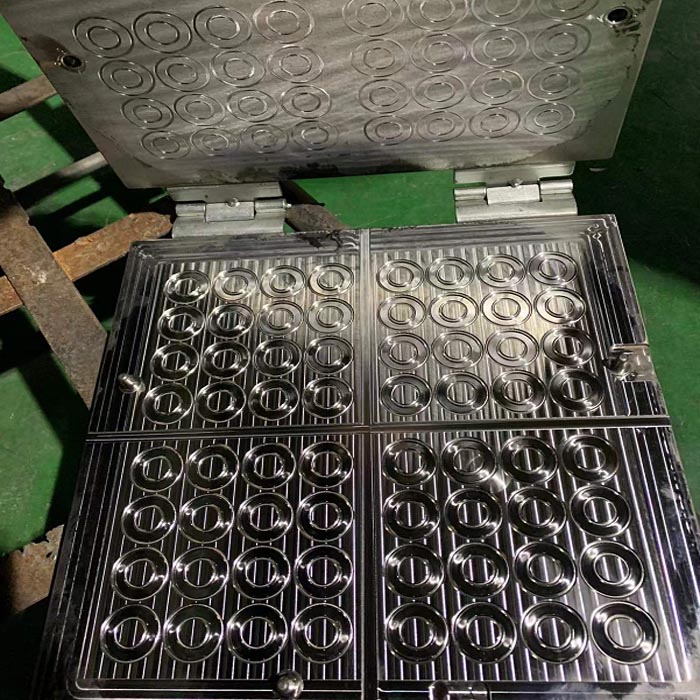
The product made from rubber as raw material and vulcanized under high temperature and high pressure with a mold is called a rubber model product. The larger one has automobile tires, and the smallest one has a lighter sealing ring with a diameter of only 50 millimeters. The mold material, dimensional accuracy, exhaust and mold opening difficulty, etc. all directly affect the quality, labor intensity, and production efficiency of rubber products. At the same time, the selection of mold material, heat treatment and other manufacturing processes, as well as the quality of mold assembly, directly affect the service life of the mold. Therefore, when designing the mold, firstly, we should carefully analyze and study the characteristics of the shape and structure of the rubber parts, and use this as a basis to select and design a reasonable mold structure, reasonable material and heat treatment process to meet the requirements of rubber products and the use of molds. It is required that the mold is easy to open after vulcanization, which can provide the production efficiency and the service life of the mold, thereby improving the economic benefit.
MB/Wechat/Whatsapp:+0086-13456489912
sophiemould@foxmail.com
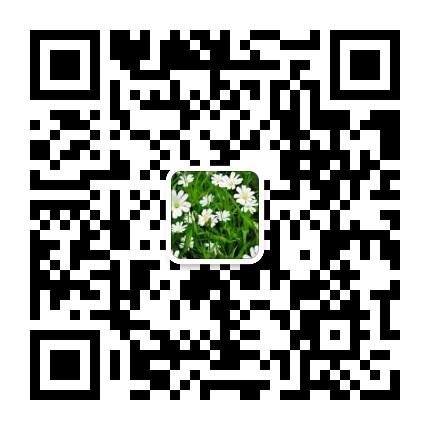
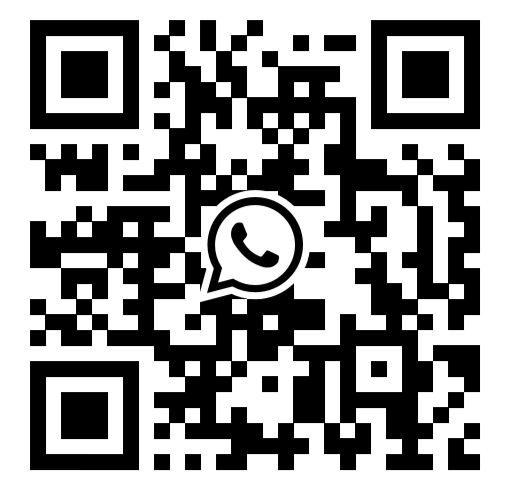
Post time: Dec-18-2021