1-The mold, or metal tooling, comprised of a cavity and a core, is installed in the press, and may feature integral heating to control temperatures throughout the process. Temperature can also be controlled from the platens of the hydraulic press.
2-Once the tool is installed and heated, fiber reinforced resin material, or the charge, is placed in the tool. The size, weight and orientation of the polymer charge will have implications on the performance of the part when completed. In some cases, the charge is pre-formed or pre-heated.
3-Once the material is in the heated cavity of the mold, the press closes at a programmed speed and pressure. When the two mold halves come together, they force the material through the entirety of the mold cavity to produce a part. The tool will remain closed, under pressure, for a predetermined amount of time based on the process requirements of the material, causing an irreversible chemical crosslink to occur which results in a cured part.
4-Once the part is cured, the pressure is released, and the part is removed from the tool. There may be a small amount of resin flash that will need to be removed.
5-Thermosets require tighter temperature controls to prevent defects and warping. Rapid cycle times prevent the material from the risks associated with pre-cure if it stays in the heated mold for too long.

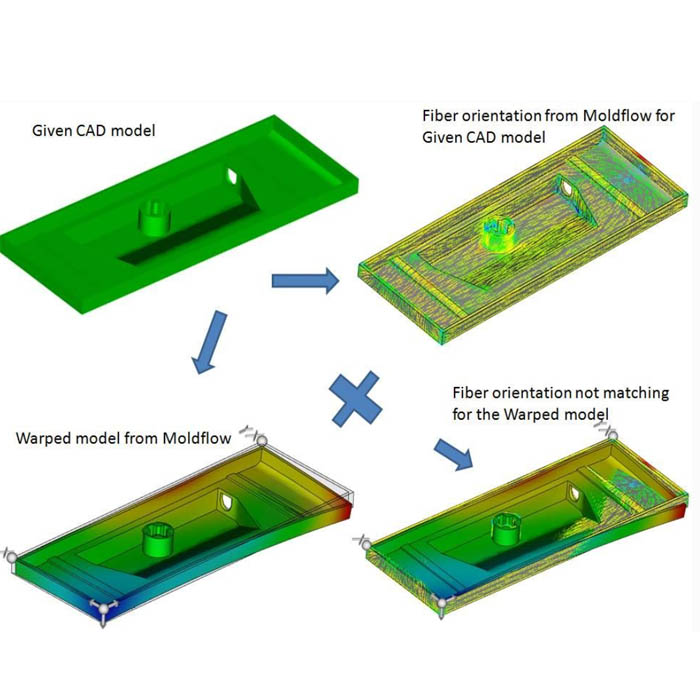
Compression molding requires a mold, which will be machined from steel or aluminum and will be designed to satisfy dimensional and tonnage requirements.
As material properties are of great importance in the compression molding process and the establishment of process parameters, the process for thermosets and thermoplastics are similar but also differ in important ways.
MB/Wechat/Whatsapp:+0086-13456489912
sophiemould@foxmail.com
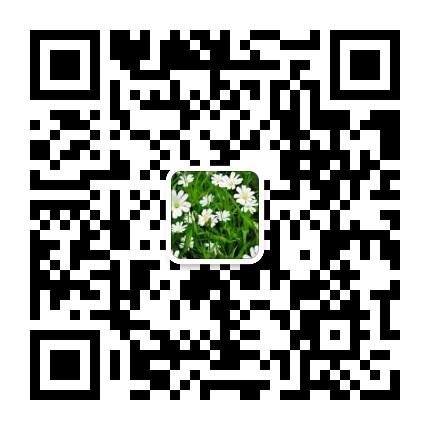
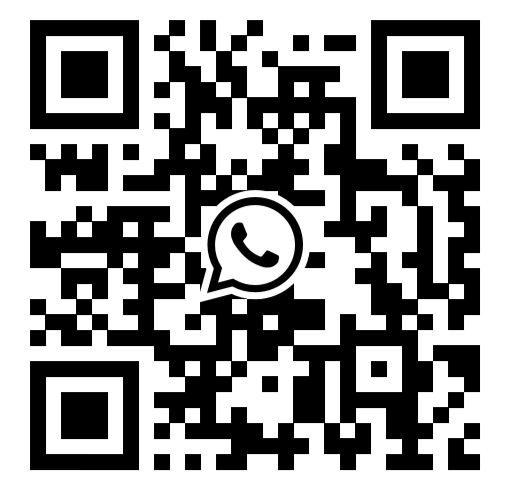
Post time: Jul-11-2021