In order to vulcanize rubber products with accurate dimensions, mold designers must be familiar with the shrinkage of various rubbers with different hardness and rubber content.
The different pressing principles of rubber products moulds can be divided into three main categories: filling molds, injection molds and injection molds.
1. Filling and pressing mold Put the rubber material into the mold cavity, pressurize, heat and vulcanize through a plate vulcanizing machine to obtain rubber products. The mold is called filling and pressing mold. The filling die can be divided into 3 kinds.
1. Open-type filling and pressing mold The open-type filling and pressing mold uses the upper and lower plates to contact, and presses the product with external force. The upper mold has no guide and no feeding cavity. The rubber is easy to flow off the parting surface, and the product has a horizontal direction. Squeeze the edges.
Open filling die
The advantages of the open-type filling and pressing die are simple structure, low cost, easy to remove air when pressing the product, but easy to lose rubber, and a large amount of rubber consumption. The mold with this structure occupies a relatively large proportion in the mold.
2. Closed filling and pressing die
The closed filling and pressing die has a feeding cavity and the upper die has a guide. During the process of pressing the product, the rubber is not easy to flow out, the rubber is under high pressure, the product is dense, and the amount of glue is small. However, the exhaust is poor, the mold requires high precision, and the manufacturing cost is also high.
Closed filling die
From the structural point of view, the semi-closed filling mold has the advantages of both an open filling mold and a closed filling mold. The fluidity of the rubber material is restricted to a certain extent when the mold of this structure forms the product, and only a part of the rubber can flow out. The pressing pressure is higher than that of the open filling mold, and the rubber product is denser.
Semi-closed filling die
b. Compression injection molding Compression injection molding is a rubber product obtained by putting rubber into a compression cavity and using the pressure transmitted by the plunger to press the rubber into the cavity through the injection port. The rubber products pressed by injection molding have high density and good product quality, which can improve production efficiency. It is suitable for manufacturing products with inserts, complex shapes, and difficult to install glue.
Insert injection mould
c. Injection Mold The injection mold uses the pressure of a special injection agent to squeeze and inject the rubber heated into a plastic state into the mold cavity after the mold is locked to form a vulcanized rubber product mold.
Injection mould
The structure of the injection mold should be determined according to the structure of the injected product, the type of injection machine, and the structure. This kind of mold is suitable for the production and use of mass products, with high production efficiency and good product quality.
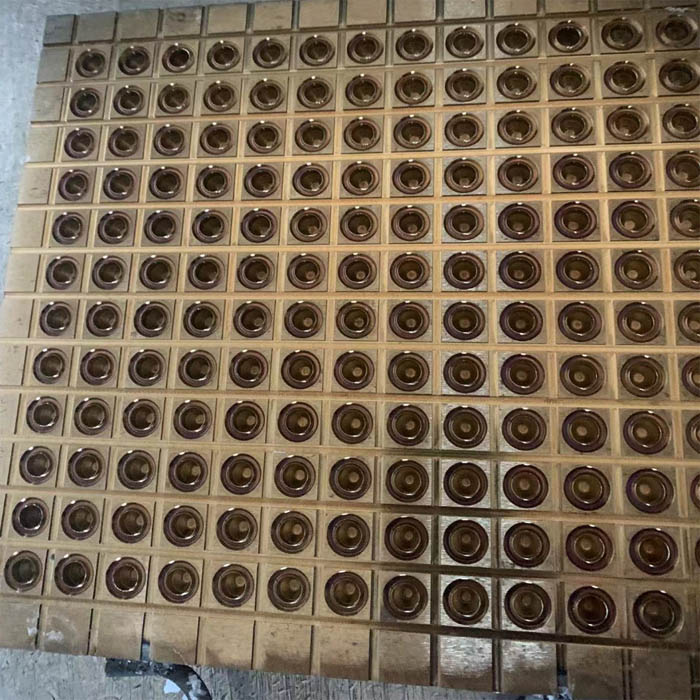
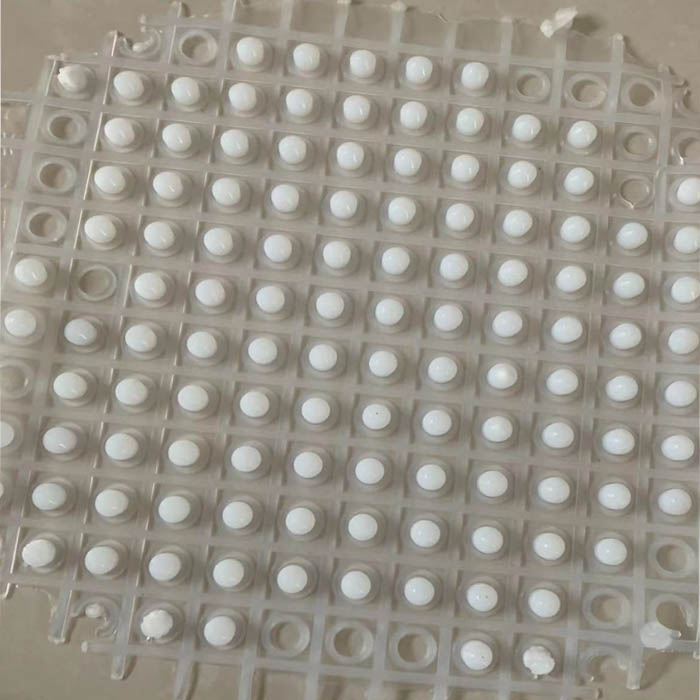
The product made from rubber as raw material and vulcanized under high temperature and high pressure with a mold is called a rubber model product. The larger one has automobile tires, and the smallest one has a lighter sealing ring with a diameter of only 50 millimeters. The mold material, dimensional accuracy, exhaust and mold opening difficulty, etc. all directly affect the quality, labor intensity, and production efficiency of rubber products. At the same time, the selection of mold material, heat treatment and other manufacturing processes, as well as the quality of mold assembly, directly affect the service life of the mold. Therefore, when designing the mold, firstly, we should carefully analyze and study the characteristics of the shape and structure of the rubber parts, and use this as a basis to select and design a reasonable mold structure, reasonable material and heat treatment process to meet the requirements of rubber products and the use of molds. It is required that the mold is easy to open after vulcanization, which can provide the production efficiency and the service life of the mold, thereby improving the economic benefit.
MB/Wechat/Whatsapp:+0086-13456489912
sophiemould@foxmail.com
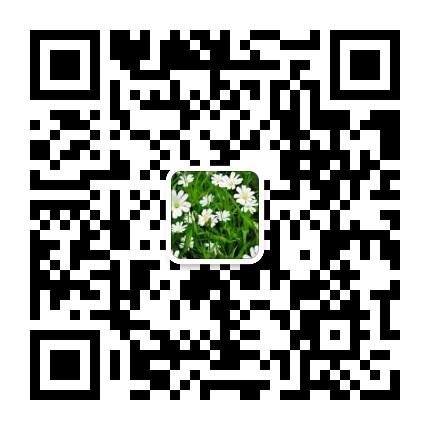
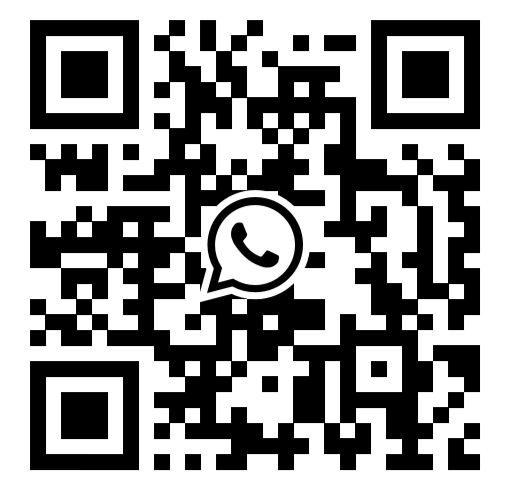
Post time: Dec-18-2021