Composite helmets are the most complicated type of helmets. They use various non-metallic materials such as glass fiber, aramid, carbon fiber, etc., to be synthesized with thermoplastic resin. Composite helmets occupies a very important position in bulletproof helmets for racing, military, and police. Generally, in developed countries, helmets are mostly made of composite materials. They are light in weight, strong in bulletproof capacity, and have a large protective area. Compared with composite helmets, they have obvious advantages. The advantages.
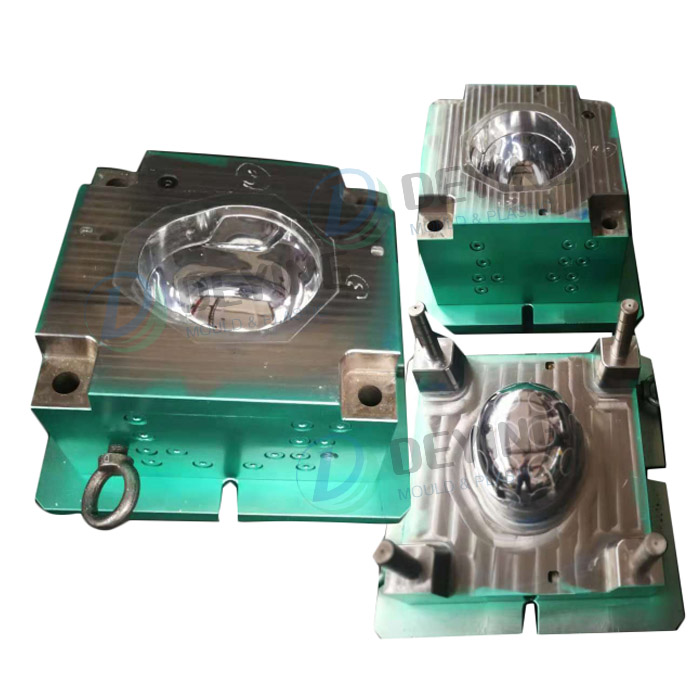
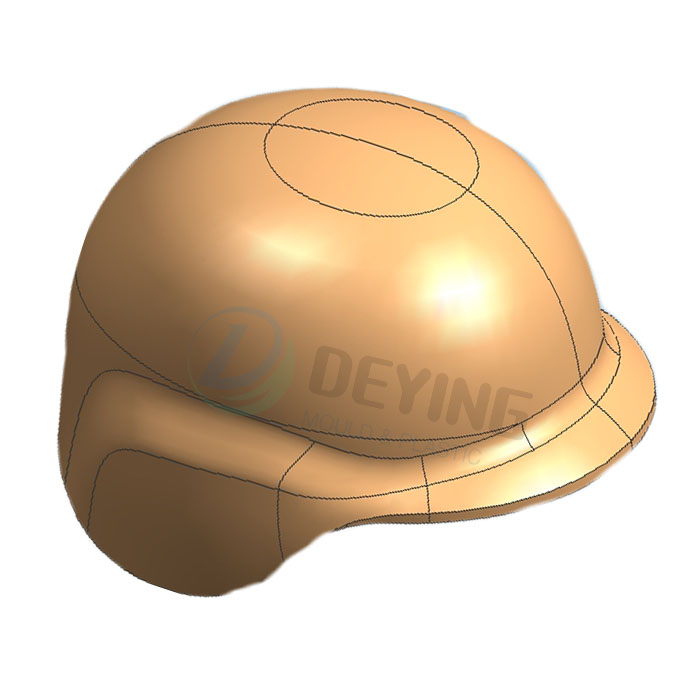
1. Key points of molding process and temperature control
The composite helmet is made of high-strength glass fiber reinforced plastic, carbon fiber, and aramid fiber. The weight is only 1/8 of that of steel. The weight is very light, and it will not feel oppressive when worn on the head. In addition, although the density of the composite material helmet is small, the strength is large. When the head is hit, it can withstand a large part of the force to protect the safety of the user. It also has low temperature resistance, fatigue resistance, abrasion resistance, UV resistance and Electrical insulation and other properties.
The molding process of composite helmets belongs to the category of plastic molding process. The main process parameters of molding include molding temperature, molding pressure and molding time. The three are related to each other and restrict each other. Whether the parameter control is appropriate or not directly affects the quality and quality of the helmet. Anti-collision and bulletproof capabilities. The temperature control system of the mold temperature machine is mainly used to control the molding temperature to ensure the best performance of the molded product.
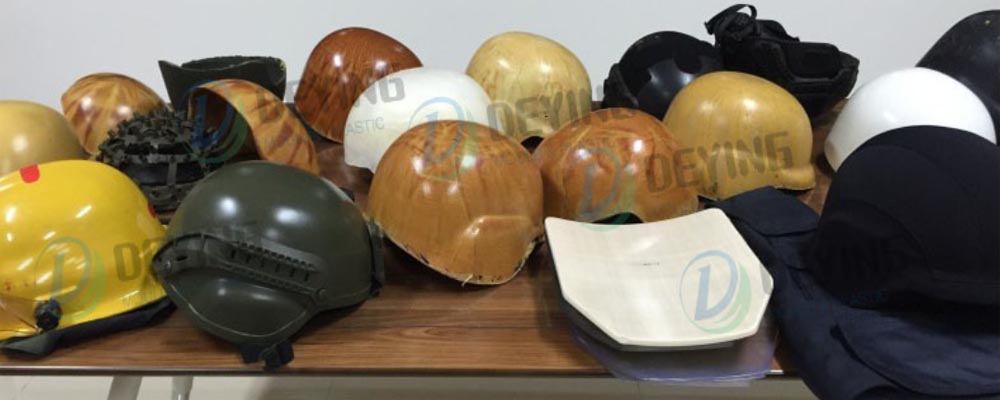
2. Mold temperature control system structure
The working process of the mold is as follows: the upper mold moves slowly down, and the laminated resin-impregnated blank (SMC) material is pressed into the cavity of the mold and maintains a certain pressure. The mold begins to heat up, and the temperature reaches 130°C and the heat preservation starts. There is an exhaust process in the middle. During the heat preservation process, the resin has a partial melting and plastic flow, so that the thickness of each part of the helmet is more uniform and the structure is more dense. After holding for a certain period of time, start the cooling system to cool the mold and shape the part. Take out the parts and perform subsequent processes such as trimming and surface treatment.
Compared with the traditional engineering plastic helmet molding mold, the composite helmet molding process requires strict temperature control, the molding thickness is large, and the molding surface is close to vertical, which makes the transmission of molding force very difficult and the molding difficult. The mold structure and temperature control system requirements are also higher.
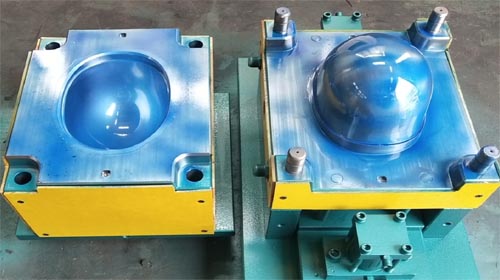
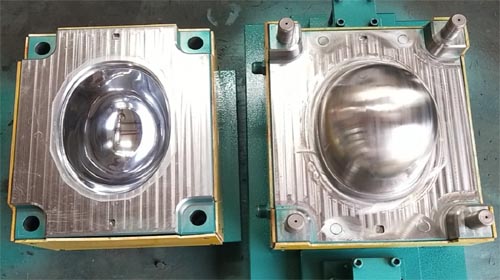
MB/Wechat/Whatsapp:+0086-13456489912
sophiemould@foxmail.com
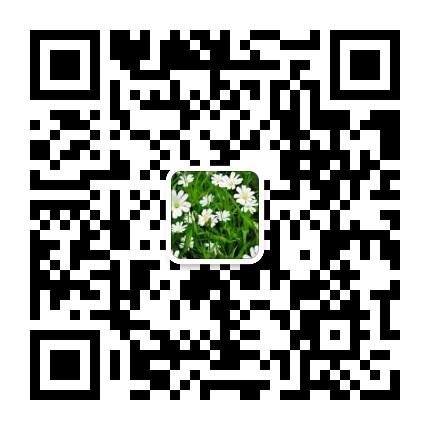
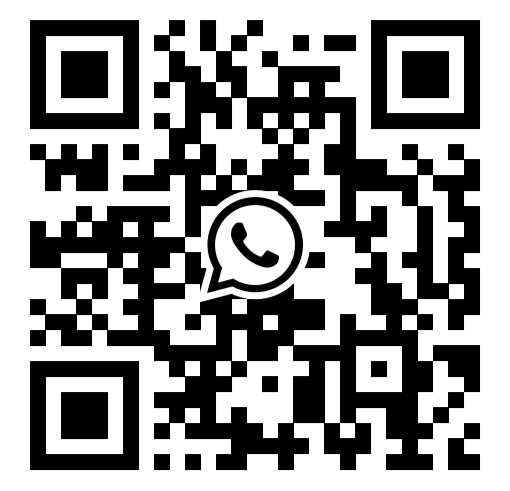
Post time: May-08-2021