Composite helmets are the most complicated type of helmets. They use various non-metallic materials such as glass fiber, aramid, carbon fiber, etc., to be synthesized with thermoplastic resin. Composite helmets occupies a very important position in bulletproof helmets for racing, military, and police. Generally, in developed countries, helmets are mostly made of composite materials. They are light in weight, strong in bulletproof capacity, and have a large protective area. Compared with composite helmets, they have obvious advantages. The advantages.
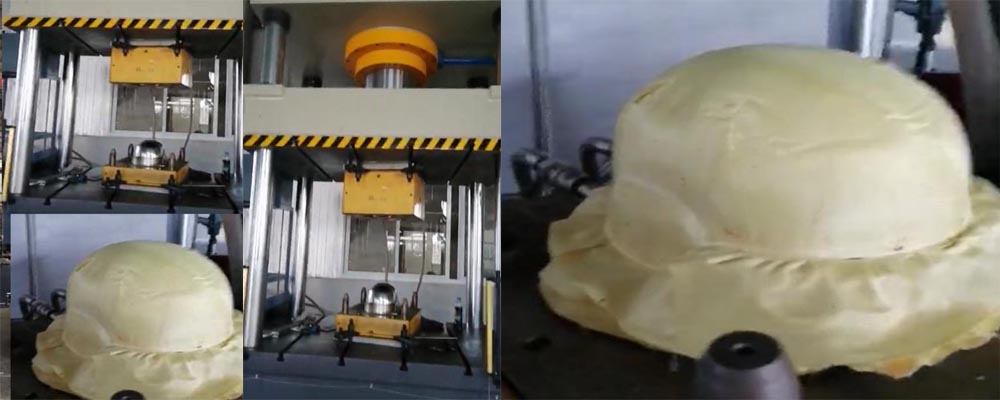
The process of Kevlar helmet mold for one-time molding of FRP helmet:
1. Cutting: According to the structure and shape of the product, the feeding position, and the process, the shape and size of the sheet cutting are determined, and the sample cutting material is made. Many cut shapes.It is square or round, and the size is usually 40%-80% of the projected area of the product surface. In order to prevent contamination by external impurities, the upper and lower films are only exposed before loading go with.
2. Weighing: the determination of the feeding amount;
3. Clean the mold: clean the mold thoroughly and apply a release agent before pressing. Wipe the release agent evenly with clean gauze before feeding, so as not to affect the product
Appearance Quality. For new molds, the oil must be removed before use;
4. Placing material: The position and method of placing material directly affect the appearance, strength and directionality of the product. Under normal circumstances, the feeding position of the material should be in the cavity of the mold Central. For asymmetric and complex products, the feeding position must ensure that the material flow reaches each end of the mold cavity at the same time during molding. Place the material method must Conducive to exhaust. When stacking multi-layer sheets, it is best to stack the material blocks in the shape of a pagoda according to the upper part and the lower part. In addition, try not to add the materials separately, otherwise,It will produce air entrapment and welding area, resulting in a decrease in the strength of the product;
5. Compression mold: When the material block enters the mold cavity, the press moves down quickly. When the upper and lower molds are anastomosed, slowly apply the required molding pressure, after a certain solidification.After the transformation system, the molding of the product is finished. During the molding process, various molding process parameters and press operating conditions must be reasonably selected;
6. Demoulding: The curing time (also called holding time) of SMC at the molding temperature and its properties, curing system, molding temperature, product thickness and color
Factors such as color are related;
7. Take out the helmet:
8. Inspection: Check whether the product is defective and qualified.
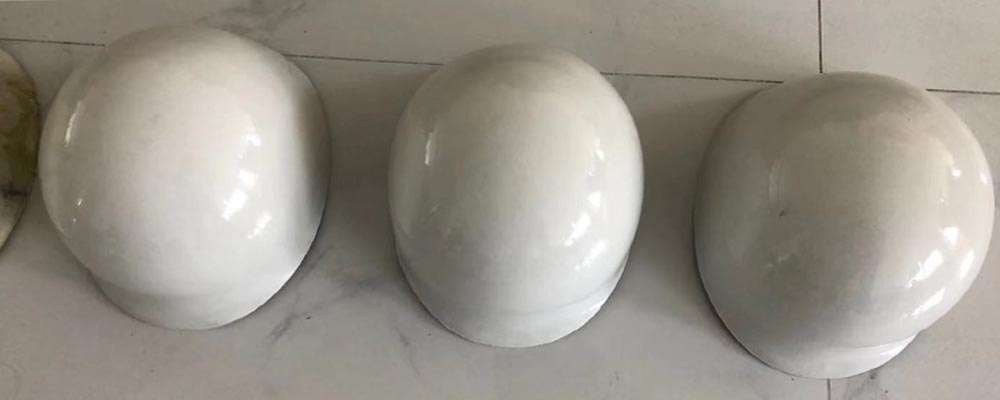
The quality of FRP helmets is very good. fiberglass helmets have high strength, good flexibility and strong impact resistance. It is a better helmet in the market today, and has advantages in all aspects than plastic helmets.
Professional glass fiber reinforced plastic helmet mold production plant,welcome contact .
Powerful manufacturer, trustworthy, welcome to contact
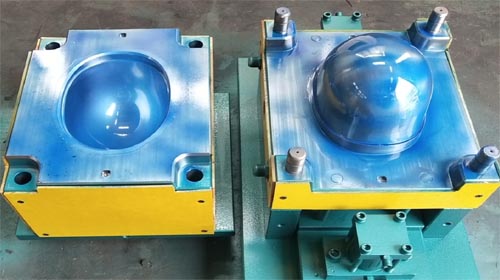
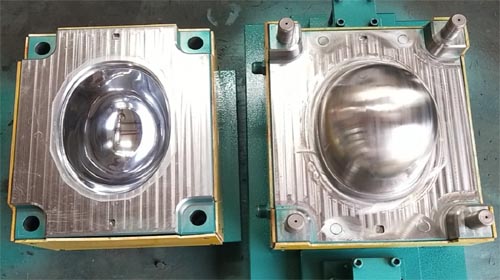
MB/Wechat/Whatsapp:+0086-13456489912
sophiemould@foxmail.com
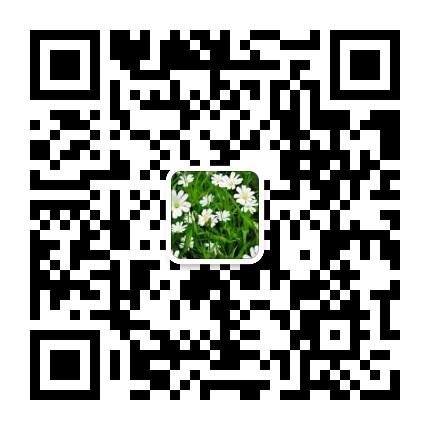
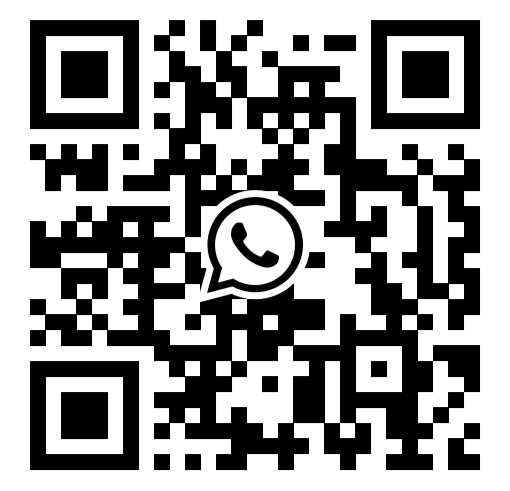
Post time: May-08-2021