The quality and performance of plastic parts is not only affected by the properties of plastic raw materials and the size of the mold structure, but also related to the formulation and control of the molding process parameters. This is the three elements of molding often referred to in production: temperature, pressure and time.
1. Molding temperature
The molding temperature refers to the mold temperature required for pressing. At this temperature, the plastic melt flows in the mold cavity, fills the cavity and solidifies and forms. The mold temperature is not equal to the temperature of the plastic melt in the cavity. For thermosetting plastics, the maximum temperature of the plastic melt is higher than the mold temperature due to the exothermic result of the plastic crosslinking reaction. When thermoplastics are compression molded, the temperature of the plastic melt in the cavity is the upper limit of the mold temperature. If the molding temperature is too high, the curing time will be short, but it will cause difficulty in filling the mold, making the surface of the plastic part dull, dull, and even swelling, deforming and cracking. If the molding temperature is too low, the curing time will be slow and the molding time will be long. Therefore, the determination of mold temperature should comprehensively consider various factors, and it is also the key to ensuring the quality of plastic parts.
2. Forming pressure
The molding pressure refers to the unit pressure of the press on the projected area of the plastic part during compression molding. Its function is to force the plastic melt to flow and fill the mold cavity to avoid defects such as bubbles and loose structure inside the plastic part due to low molecular volatiles, ensure that the plastic part has a fixed shape and size, prevent deformation, and improve the internal quality.
3. Time
When thermosetting plastics are compressed and molded, they need to be kept at a certain temperature and pressure for a certain period of time to be fully crosslinked and solidified to become a good plastic part. This period of time is called compression time. The compression time is related to the type of plastic (type of resin, volatile content, etc.), shape of the plastic part, process conditions (temperature, pressure) of compression molding, and operation steps (whether venting, pre-pressing, pre-heating), etc. When the compression molding temperature increases, the plastic solidifies faster, and the required compression time is reduced: an increase in compression pressure will also reduce the compression time, but it is not as obvious as the increase in temperature. In addition, the compression time will increase as the wall thickness of the plastic part increases. The length of compression time has a great influence on the performance of plastic parts. The compression time is too short, the plastic is not hardened enough (under-ripe), the appearance quality of the plastic part is poor, the mechanical properties are reduced, and it is easy to deform. Appropriately increasing the compression time can reduce the shrinkage of plastic parts and improve their heat resistance and other physical and chemical properties. However, if the compression time is too long, it will not only reduce the productivity, but also cause the plastic parts to shrink too much, increase the internal stress, and easily break the plastic parts. Generally, the compression time of phenolic plastic is 1~2min, and that of silicone plastic is 2~7min.
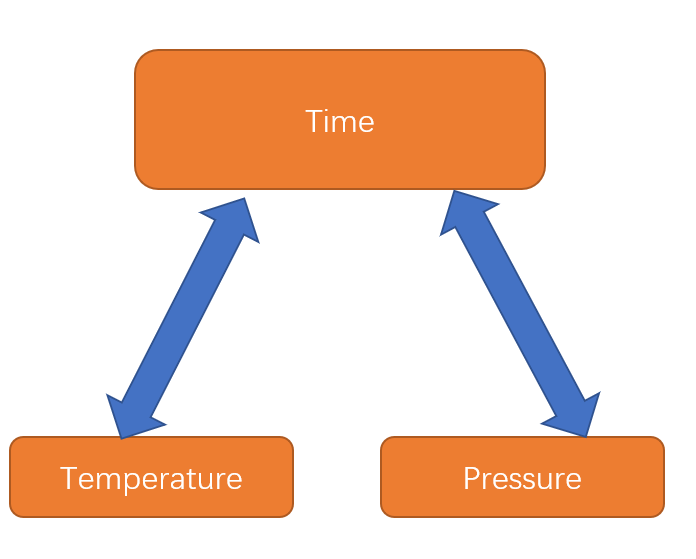
Characteristics and application of BMC mold
BMC, is the abbreviation of Bulk molding compounds, that is, bulk molding compound. It is a mixture of various inert fillers, fiber reinforced materials, catalysts, stabilizers and pigments to form an adhesive "putty-like" composite material for compression molding or injection molding. Bulk molding compound (BMC) is highly filled and reinforced by short fibers. Glass fiber reinforced material accounts for 10% to 30%, and the length is usually between 1/32 inch and 1/2 inch (12.5mm).
BMC has many unique characteristics, such as high hardness, light weight, corrosion resistance, UV resistance, good insulation, and excellent thermal properties, which make BMC more satisfactory than thermoplastics. At the same time, since many components can be molded simultaneously with these components, no post-processing is required, which is more economical from a production point of view.
Because BMC material has good physical, electrical and mechanical properties, it has a wide range of uses. For example, we can use BMC material to make gearbox components, valve valves, bumpers and other mechanical parts; in earthquake-resistant buildings , Beautiful furniture and durable aviation and other fields have also been widely used; and in traditional household appliances, catering services, etc., BMC materials are gradually playing its role.
DEYING mold, as a professional mold manufacturer, can meet any of your needs, welcome to contact us.
MB/Wechat/Whatsapp:+0086-13456489912
sophiemould@foxmail.com
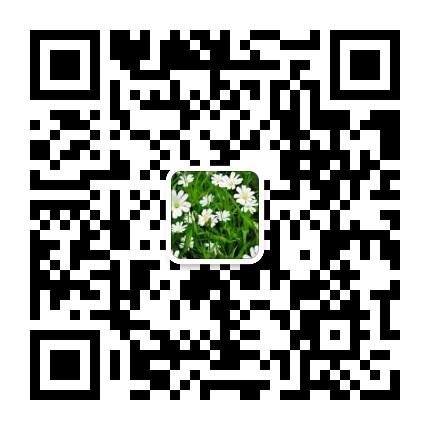
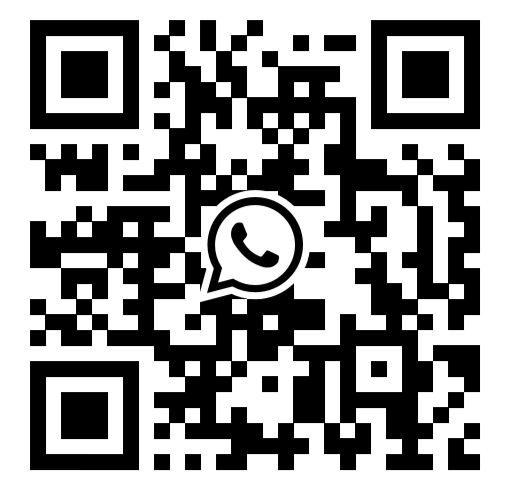
Post time: Jul-23-2021