Composite materials
Composites, such as laminated plastics, are also thermosets that are utilized in the compression molding process. Laminated plastics are a special form of polymer-matrix composite that is comprised of layers of fiber reinforced materials that are impregnated with thermosetting resins (typically phenolics), bonded together using heat and pressure. Once the material is impregnated and dried, it is cut into sheets, stacked together, and pressed using high pressure and specified temperatures (270° to 350°F). This results in a laminated composite that can range from hard materials to softer plasticized grades, depending on the application.
Sheet molding compound (SMC)
Sheet molding compound (SMC) is a fiber reinforced thermoset material (a combination of polymer resin, inert fillers, fibers, catalysts, pigments, stabilizers, release agents and thickeners) often used for larger parts that require greater mechanical strength. Glass reinforcement is between 10 and 60 percent and fiber length is slightly longer than those of bulk molding compound (BMC), between ½-inch and 1-inch.
The manufacturing process of SMCs is a continuous in-line process where the material is sheathed both top and bottom with a polyethylene or nylon plastic film to prevent auto-adhesion. The paste is spread uniformly onto the bottom film, the chopped fibers are added on the paste in a random fashion and the top film is introduced to the process, rolled into a pre-determined thickness and left to mature for 48 hours.
SMC satisfies applications that produce appearance critical parts that have a Class A finish, but it is also ideal for painting and structural applications that require strength and stiffness, but not an appearance critical aesthetic.
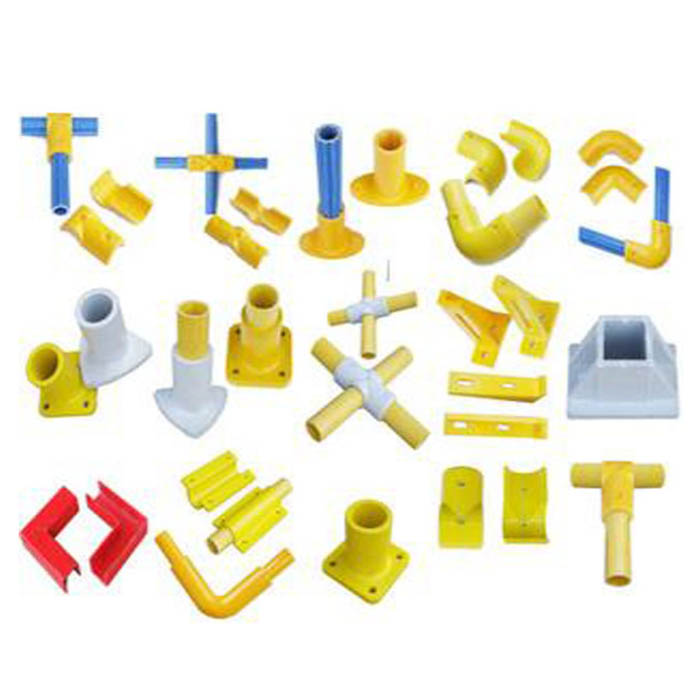
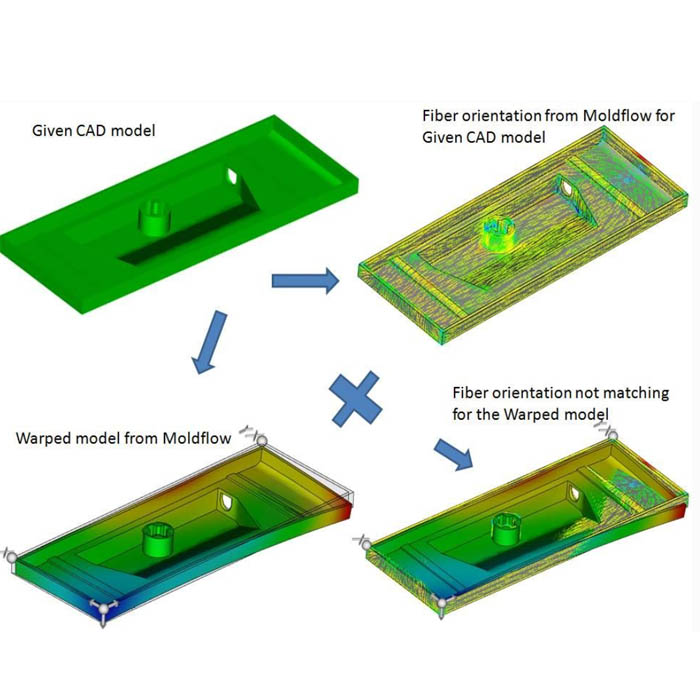
Bulk molding compound (BMC)
Bulk molding compound (BMC) is a thermoset plastic resin that is similar to SMC but the way in which the fibers and the resin are combined differs. It is still a blend of inert fillers, fiber reinforcement, catalysts, stabilizers, and pigments, but they form a viscous putty. The material is highly reinforced using short glass fibers, with a glass reinforcement measure of 10 to 30 percent, with lengths between 1/32-inch and ½-inch.
BMCs will achieve close dimensional control, flame and track resistance, electrical insulation, corrosion and stain resistance, in addition to heightened mechanical properties, minimized shrink capacity, and color stability which make it ideal for applications requiring precision in detail, dimension and performance. It can also tolerate powder coating and water-based paint.
Thermosets, in general, offer excellent flame, smoke and toxicity characteristics. A great example is cyanate ester which boasts extremely low out gassing attributes. They also promise low density, corrosion resistance and dielectric characteristics. They are cost-effective and offer design flexibility that many projects yearn for.
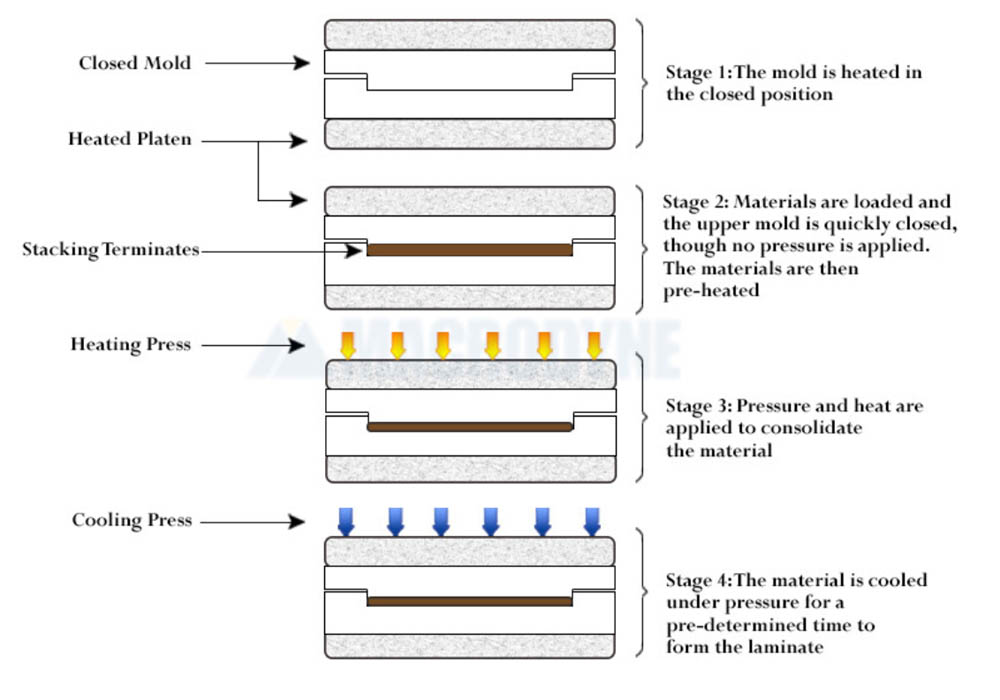
Laminated thermosets offer high mechanical strength, dimensional stability, rigidity, a high strength-to-weight ratio, as well as good electrical, moisture and temperature resistance. During the production process of these multilayer materials, it is important that fibers are thoroughly wetted with resin, with the excess resin removed.
Laminate needs to be consolidated to thickness and all trapped air, moisture and solvent vented to avoid porosity in the material. Curing time is imperative to ensure the material is neither over-, nor under-cured.
Applications for these laminated composite materials include switchboard panels and terminal boards, starter/generator/television insulation, gaskets, washers, gears, or any other product where high feeding and cutting speeds are present.
Cured laminates, also referred to as high-pressure laminates, are produced in over 70 standard grades in compliance with National Electrical Manufacturers Association (NEMA) specifications. The same base materials can be found in molded-laminates and molded-macerated parts where mold costs are justified by production quantities and where machining from flat laminates is uneconomical.
MB/Wechat/Whatsapp:+0086-13456489912
sophiemould@foxmail.com
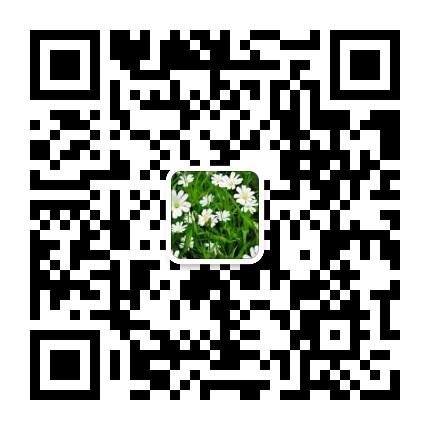
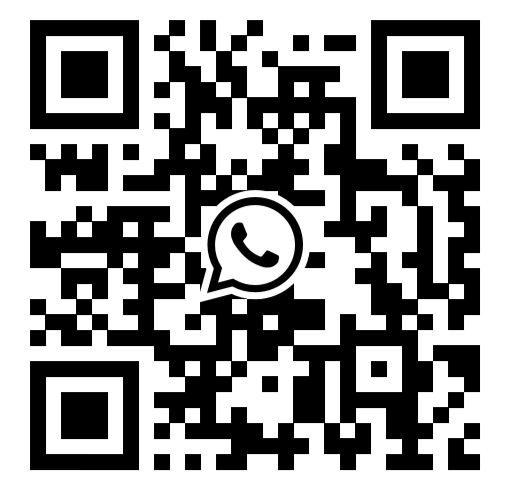
Post time: Jul-11-2021