Compression molding produces composite parts of varying complexities that are comparable to those manufactured from metal. They offer the same strength and mechanical properties but outperform metals in their weight-to-performance ratio, anti-corrosive and electrically insulative properties, and require less post-fabrication machining to meet geometric specifications.
One of the greatest advantages of the compression molding process is the ease at which ribs, and other inserts can be incorporated at the time of forming which reduces or completely eliminates the need for secondary processes. With one process, it can replace several assembled parts with one complex compression molded part.
The ability to incorporate secondary processes reduces the need for labor and parts inventory and minimizes material scrap and inspection times. Another benefit is the low tooling cost and the need for less costly capital equipment, as well as the fact that it is adaptable to automation. All of these things result in cost savings without compromising performance, quality, and output.
Shortfalls of compression molding are that the process is not ideal for very intricate parts or parts containing undercuts, side draws, or small holes, as it runs the risk of producing small distortions or breaks as a result of the process flow and pressure. From a process perspective, compression molding rivals injection molding in most ways, except in terms of cycle times which are longer on account of heating and cooling processes, which are paramount to part performance and quality when using thermosets and thermoplastics in the compression molding process.
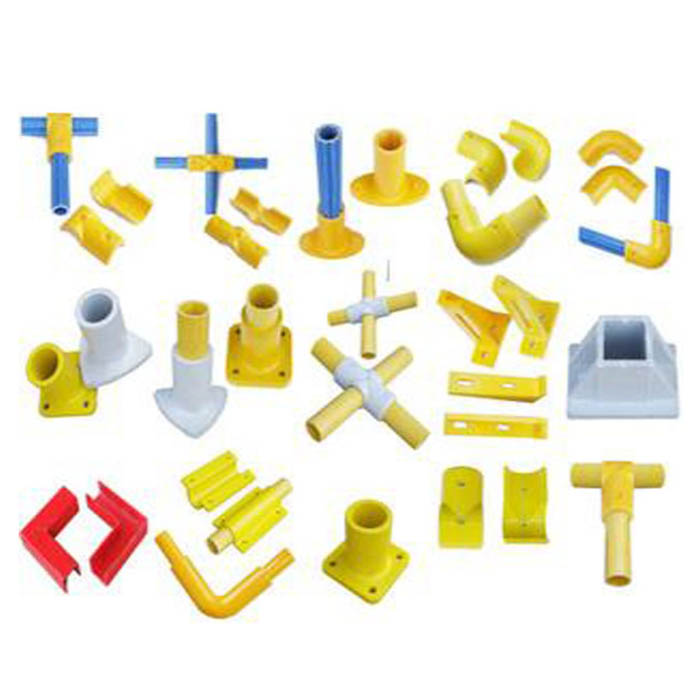
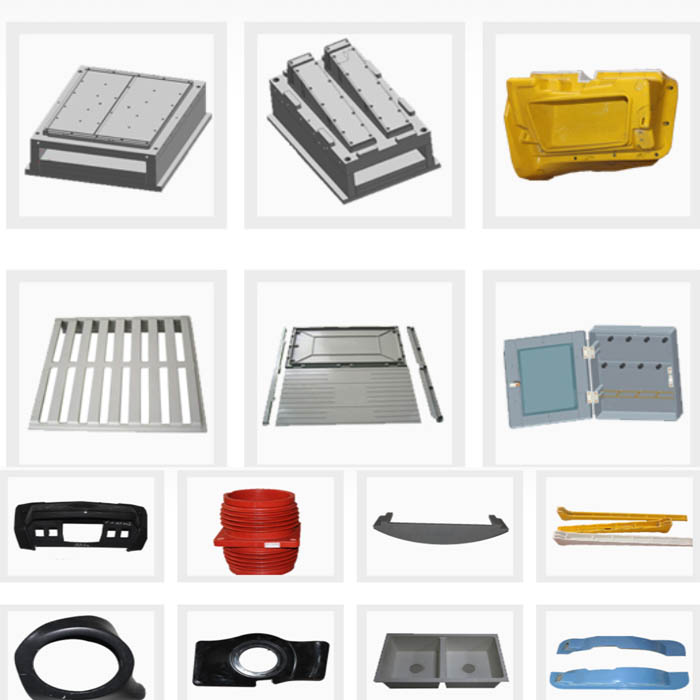
Advantages of DEYING compression mould:
1. Rich experience and sufficient early communication to ensure that the mold plan is in place as soon as possible, reduce later revisions, and make the mold cycle faster!
Second, a good and uniform heating scheme and thermal cycle system can greatly reduce the deformation of the product, and make the product production faster and more stable.
3. Good processing equipment and strict processing control procedures ensure that the flash of the product is within the controllable range and reduce the workload of later workers.
Four high-quality mold parts and reliable mold materials, mature heat treatment process, to ensure the stability and continuity of mold production.
DEYING molds, diligently, create excellent quality!
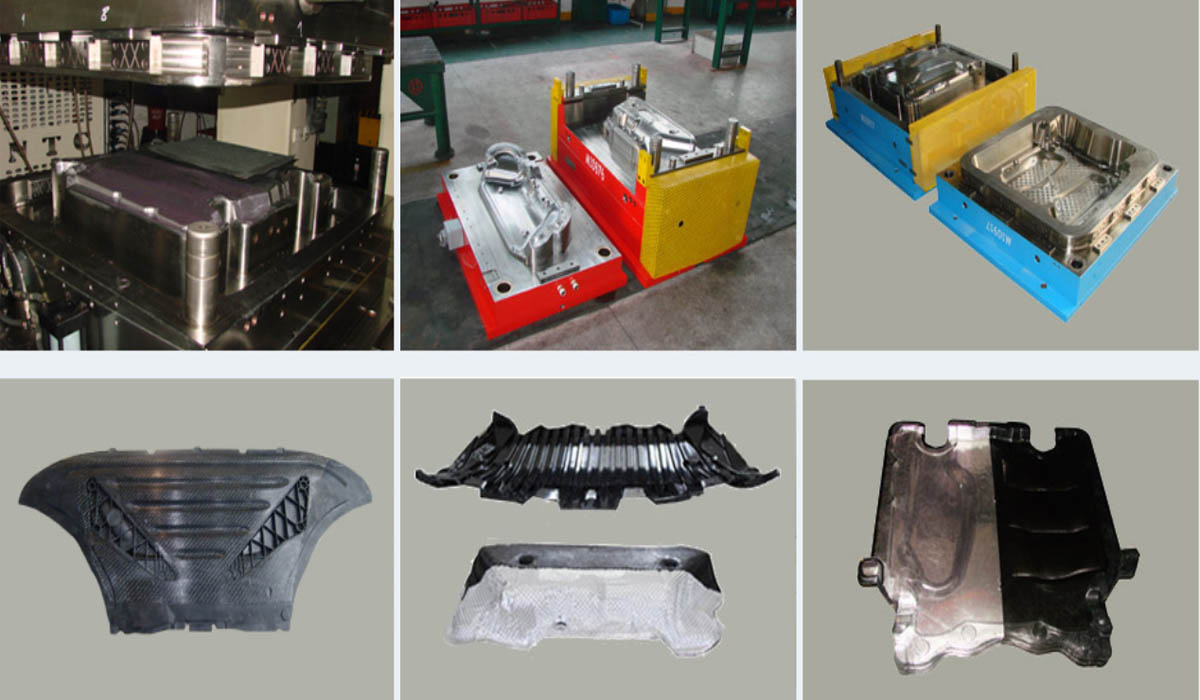
Thermoset composites are the most common type of material used in the compression molding process. Thermosets include Bakelite, polyester, polyurethane, urea-formaldehyde, as well as melamine, epoxy, and alkyd resins.
Thermoset materials are selected based on their properties, the application, and the associated costs. For example, vinyl ester resin utilized for its for corrosion resistant applications, while epoxy resin satisfies the design requirements of high-strength applications and polyester resin is usually selected for both cost and performance factors.
Utilizing thermosets in the compression molding enables manufacturers to achieve complex geometries and parts that mimic the properties of metal with several additional advantages. The strength-to-weight ratio it offers is ideal for applications like automotive parts, as they produce lighter, durable components that will not add significantly to the weight and performance of the vehicle.
While strength and structural integrity are certainly competitive advantages of thermosets, its downfalls include poor elasticity and elongation. Its low initial viscosity can result in flash and the need for secondary machining operations. It also tends to be more difficult to surface finish. Likewise, high levels of some fillers can lead to excessive tool wear.
When molded, the resulting structure of the material is highly crosslinked, comprised of heavily branched molecules, chemical bonds that promote high mechanical and physical properties. As a result, it cannot be recycled like its thermoplastic counterparts. Thermosets are selected where the strength and quality of the part is dependent on the degree of crosslinking that takes place
MB/Wechat/Whatsapp:+0086-13456489912
sophiemould@foxmail.com
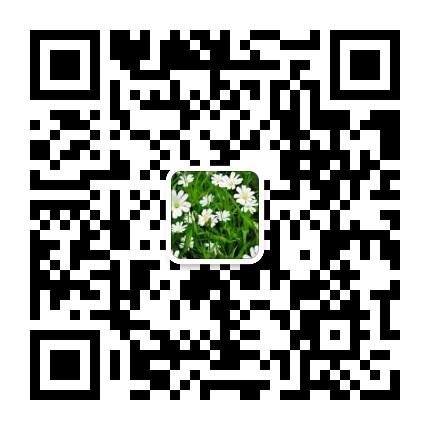
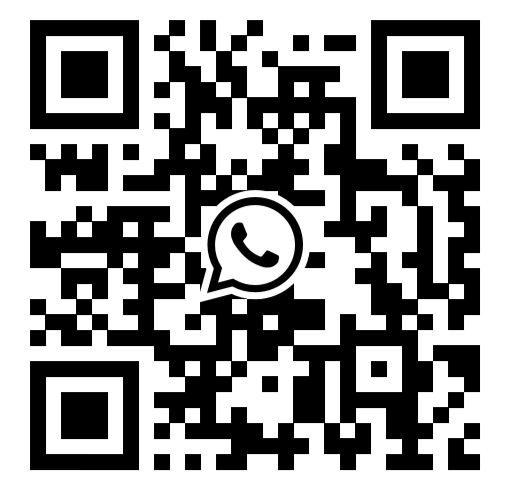
Post time: Jul-11-2021