These bulletproof kevlar helmet mould made by DEYING Mold factory in taizhou huanyuan,the characteristics of the moulded moulds we produce: high production efficiency, continuous working of moulds, long service life, and labor saving.
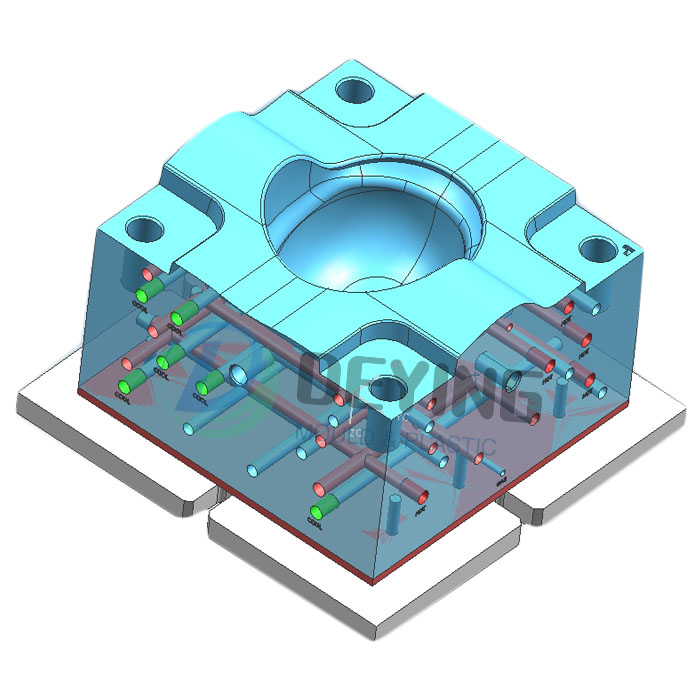
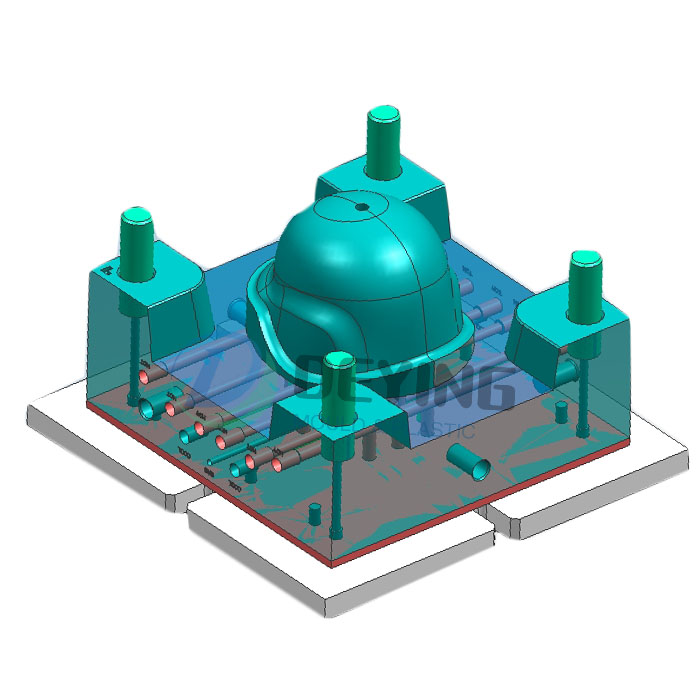
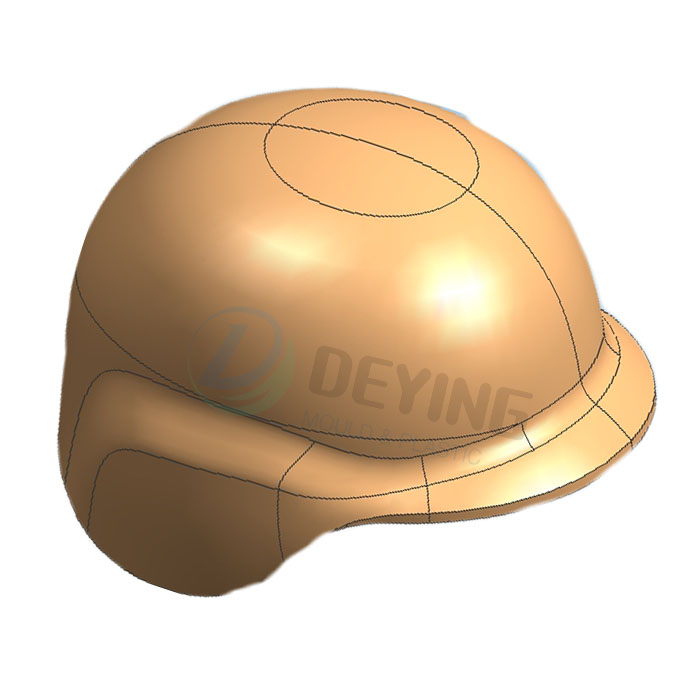
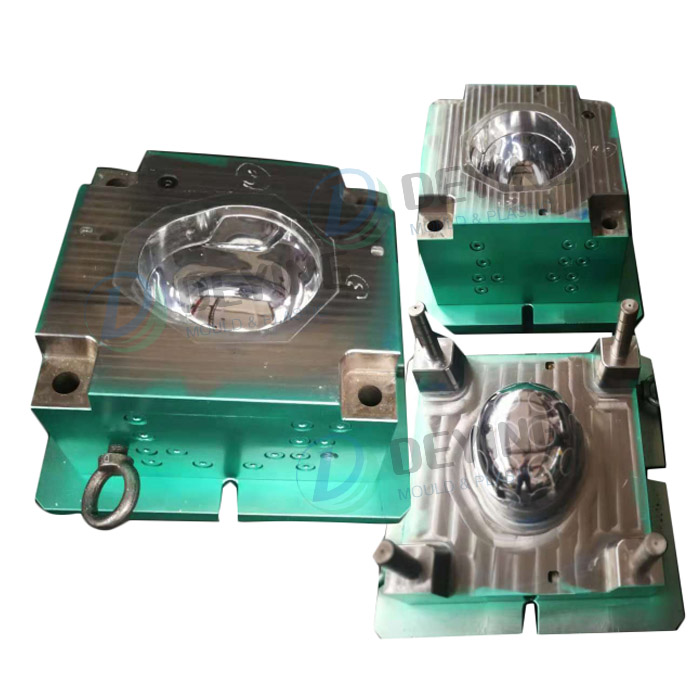
There are many factors that affect the mold structure and individual mold systems, and they are very complex:
1. Cavity layout. Determine the number of cavities and their arrangement according to the geometric structure characteristics of FRP parts, dimensional accuracy requirements, batch size, mold manufacturing difficulty, mold cost, etc.
For the pressing mold, the precision of FRP parts, the temperature control method, the curing time and the sequence of actions, etc.
2. Determine the parting surface. The position of the parting surface should be conducive to mold processing, venting, demolding and forming operations, and the surface quality of FRP parts.
3. Determine the cloth method (shape, position, size of SMC, DMC, BMC) and exhaust system (exhaust method, position and size of exhaust slot).
4. Select the ejection method (ejector, pipe, push plate, combined ejector), determine the undercut treatment method and core pulling method.
5. Determine the cooling and heating method, the shape and location of the heating and cooling groove, and the installation location of the heating element.
6. According to the mold material, strength calculation or empirical data, determine the thickness and dimensions of the mold parts, the shape structure and all the connections, positioning and guide positions.
7. Determine the structure of the main forming parts and structural parts.
8. Considering the strength of each part of the mold, calculate the working size of the molded part.
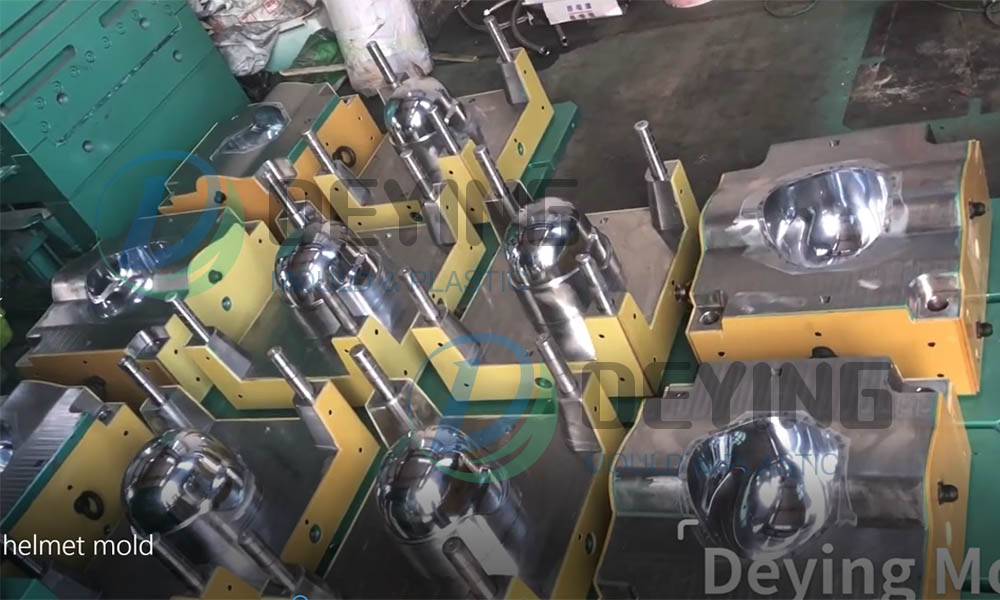
Compression molding is a method of molding in which the molding material, generally preheated, is first placed in an open, heated mold cavity. The mold is closed with a top force or plug member, pressure is applied to force the material into contact with all mold areas, while heat and pressure are maintained until the molding material has cured.
UD/KEVLAR product mould
UHMWPE is commonly known as very high molecular weight polyethylene. Its molecular weight can reach 1 to 5 million. It has high wear resistance, low friction coefficient, high impact resistance, and better sound-absorbing performance. Compared with ordinary thermoplastics, it has lower fluidity and is difficult to process. At present, it can only be produced by molding. Our company cooperated with the *** unit, using its good impact resistance, developed the body armor and bulletproof helmet molds, realized segmented pressurization and heating on a pair of molds, and switched the heating mold to cooling in the later stage of molding. The mold ensures that the product is cooled and shaped to the set temperature and set material hardness, ensuring that the product can be easily taken out of the mold.
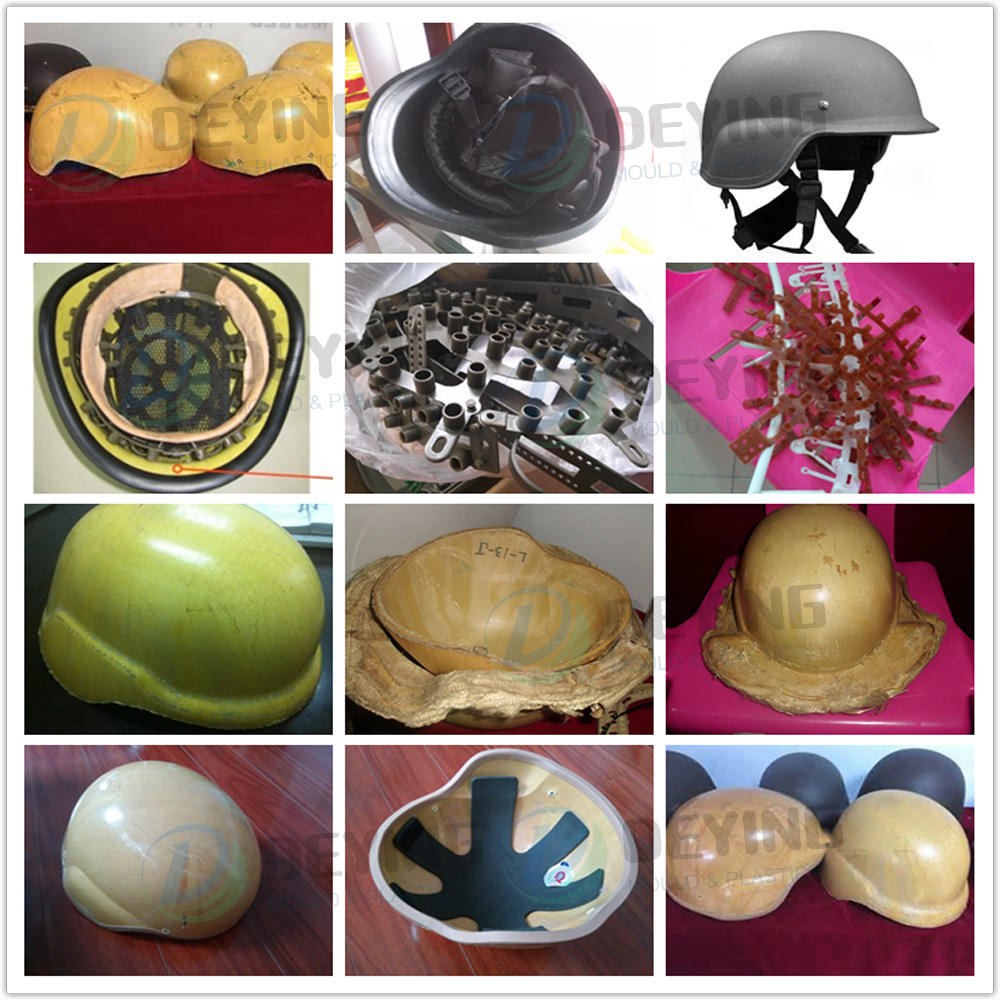
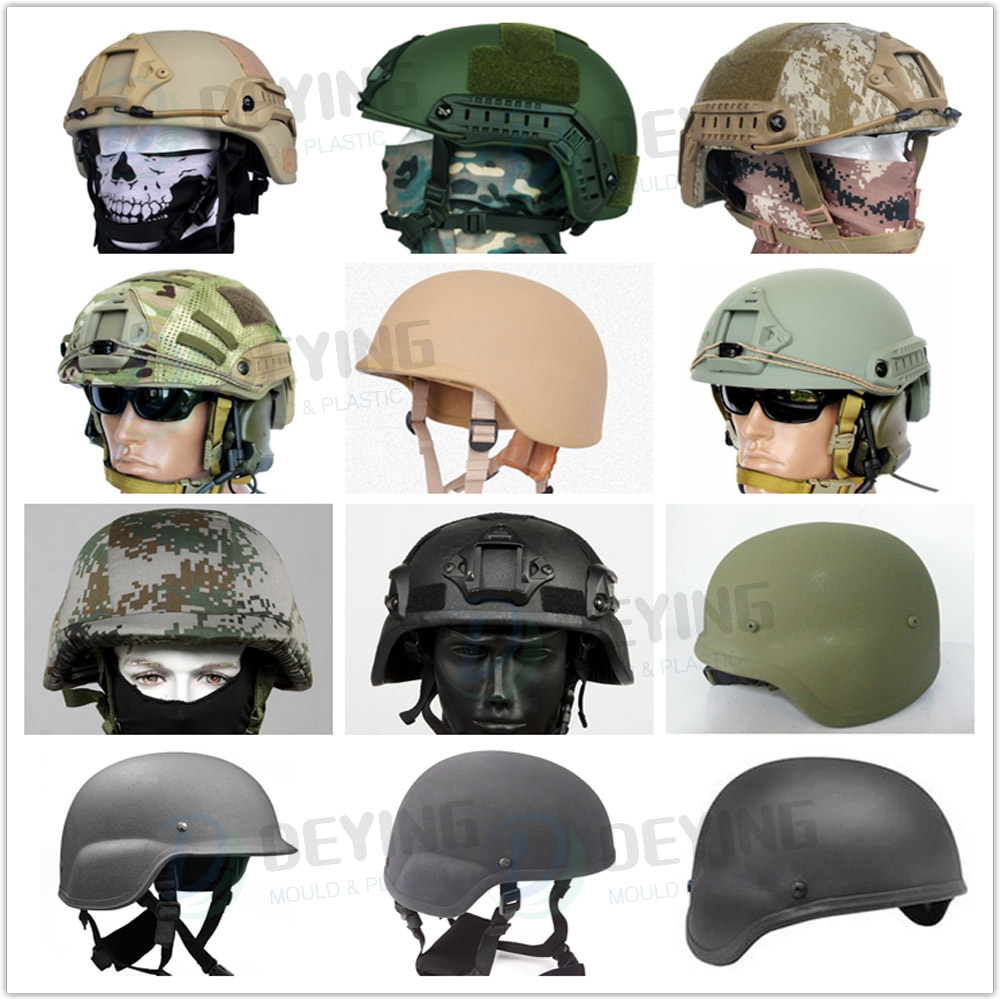
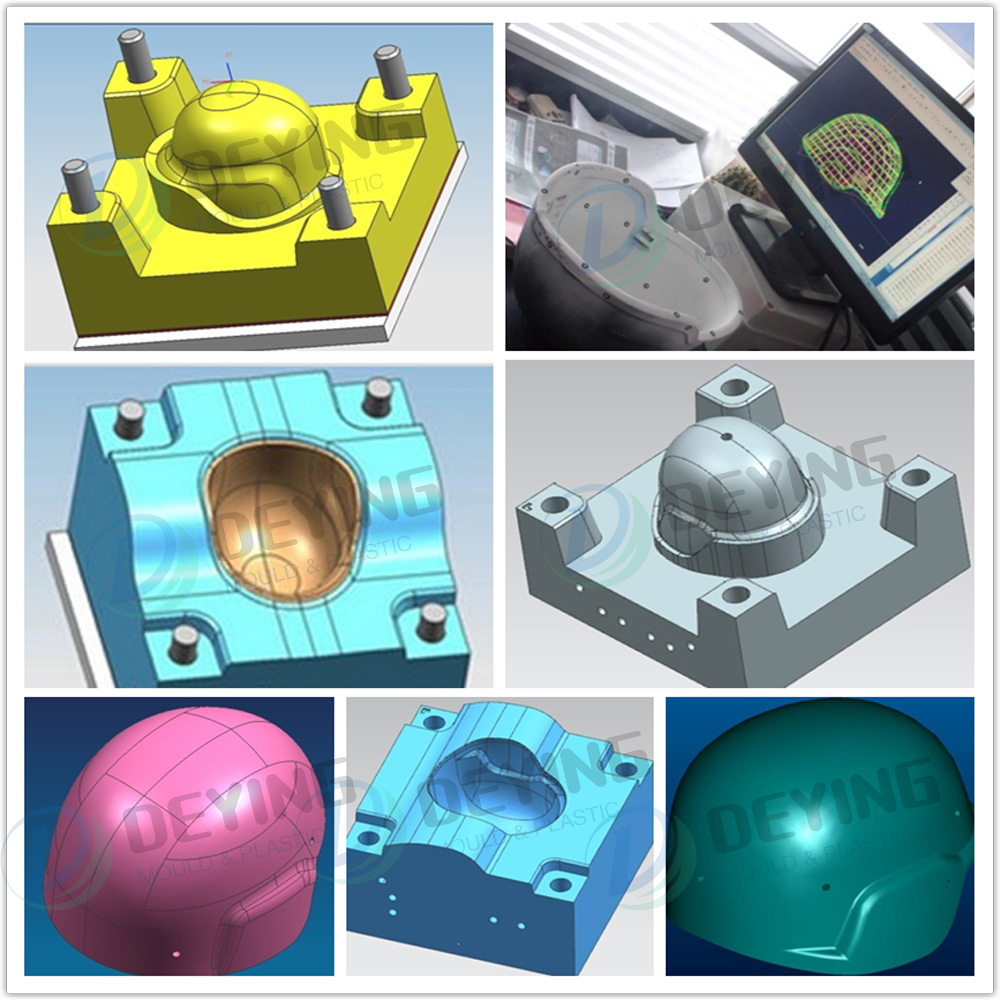
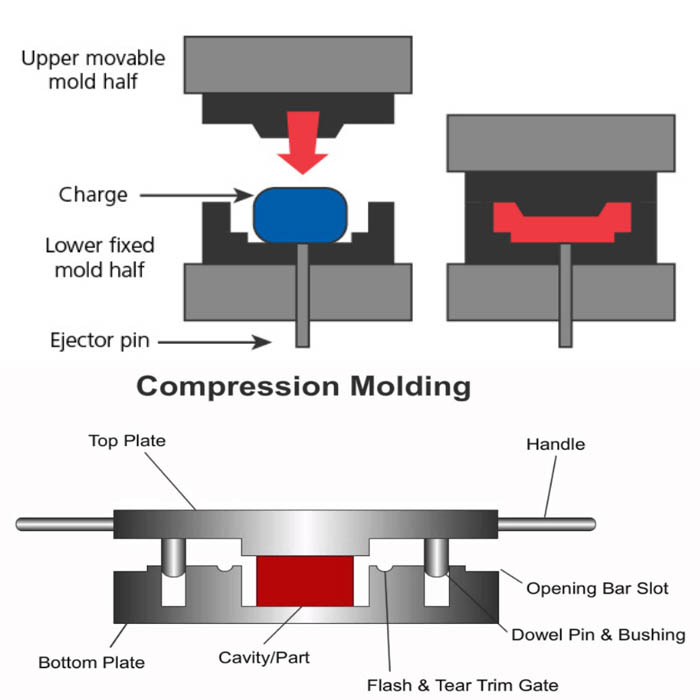
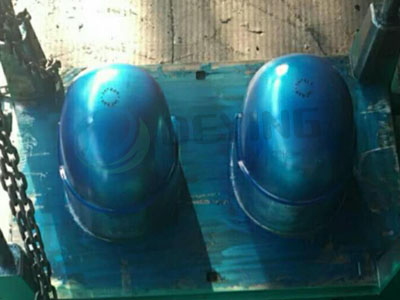
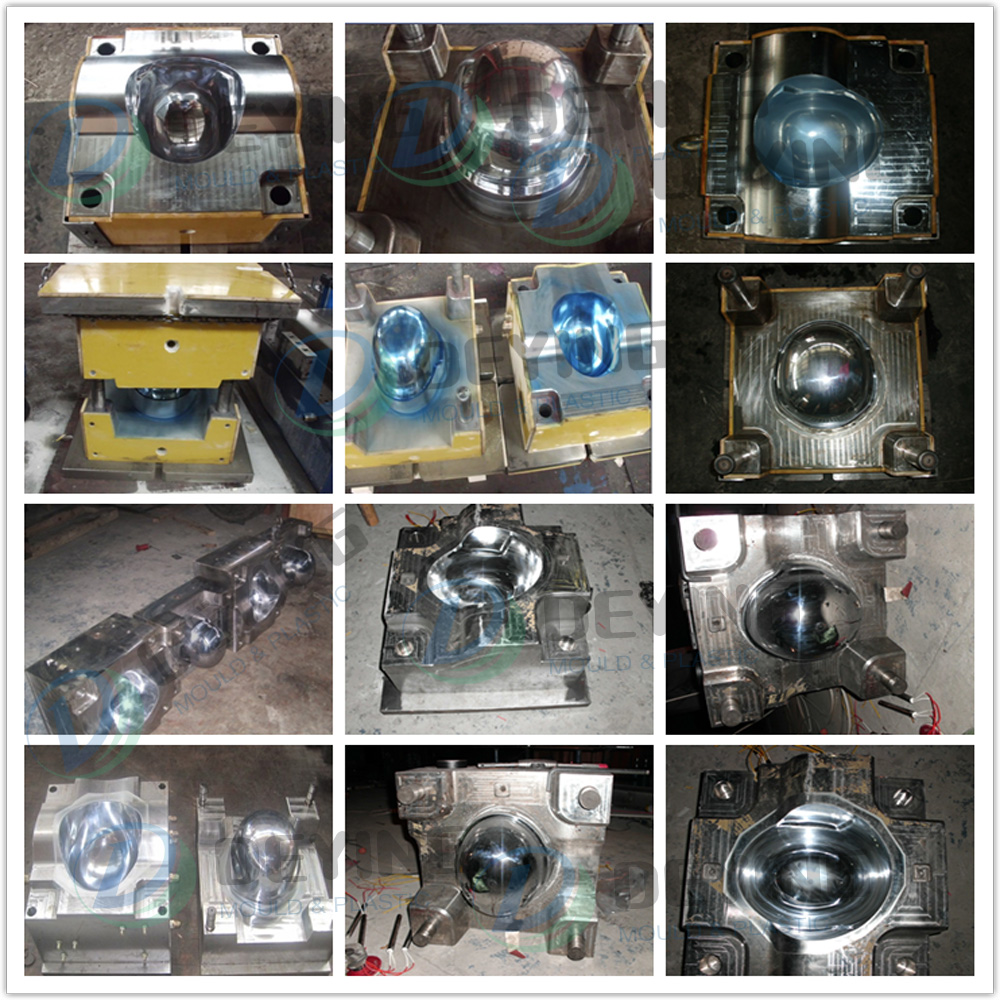
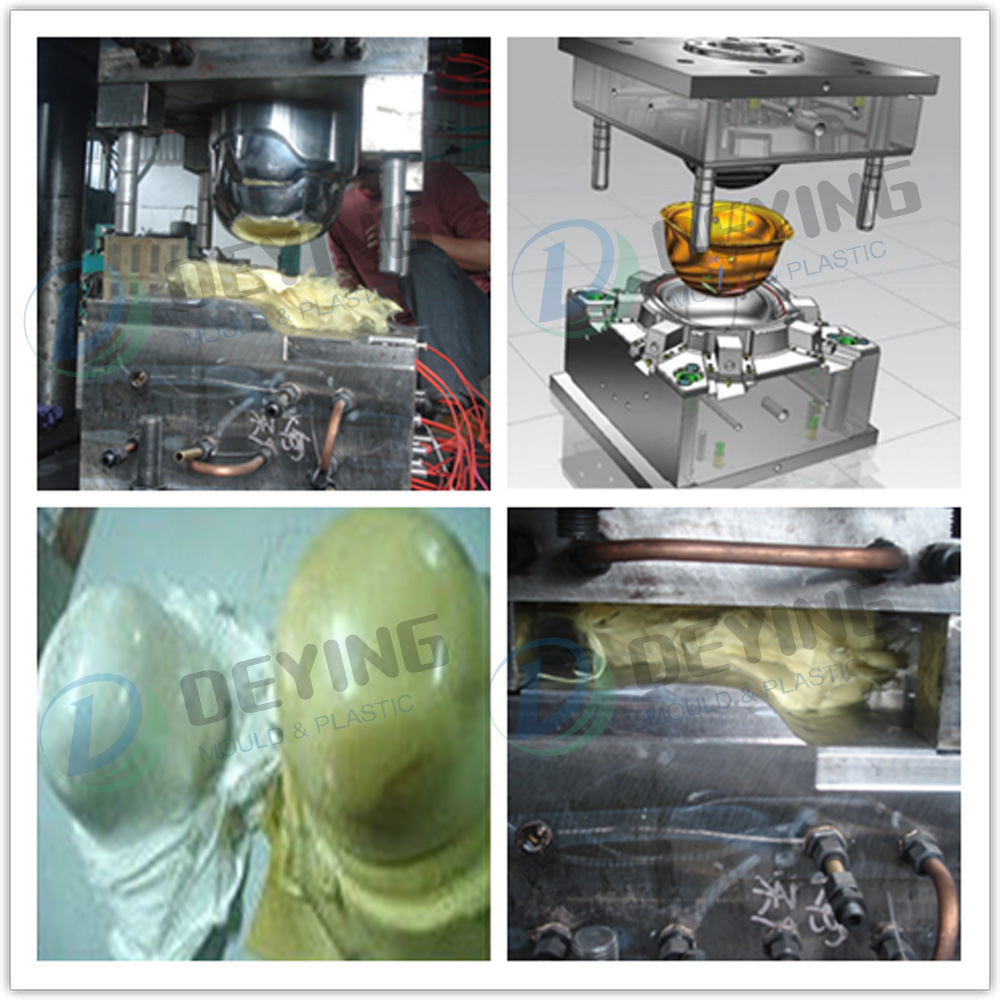
MB/Wechat/Whatsapp:+0086-13456489912
sophiemould@foxmail.com
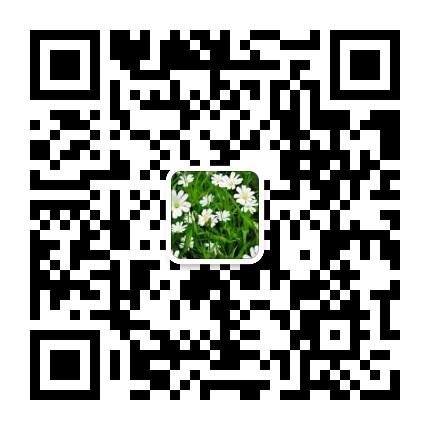
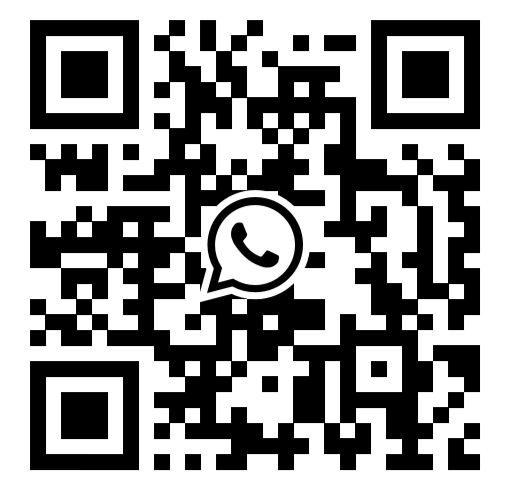